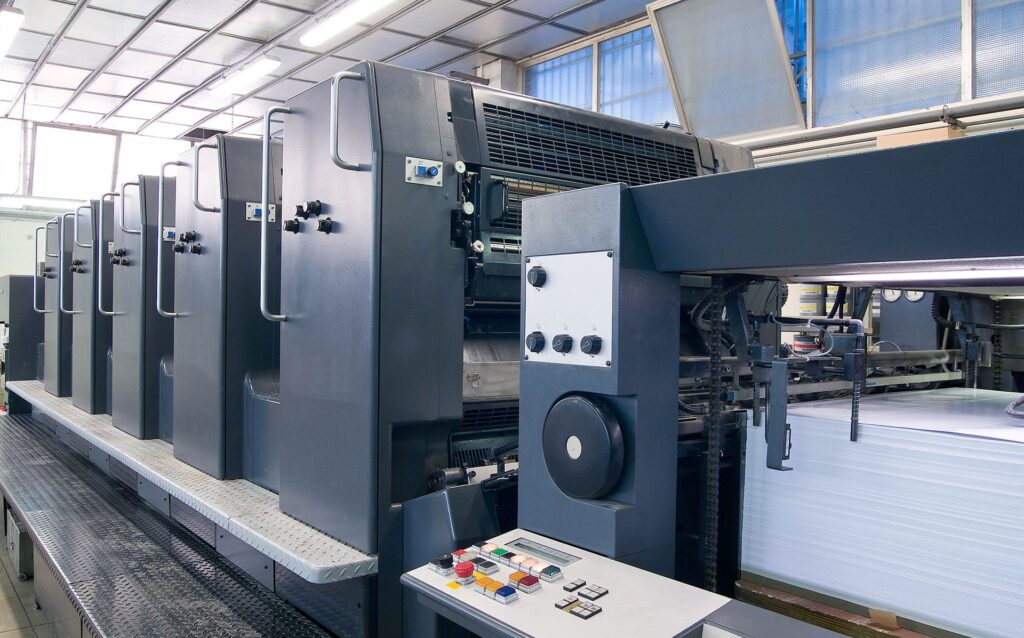
Printing 101: What is Offset Lithography
Offset lithography, a widely used printing technique, forms the backbone of traditional commercial printing. Born in the late 19th century, this method has stood the test of time, proving to be a reliable and efficient means of reproducing high-quality images on various surfaces. At its core, offset lithography involves the principle of oil and water repulsion, harnessing the chemistry between ink and water to transfer images from a plate onto a rubber blanket before finally being imprinted onto paper or another material.
What is Offset Lithography
At its core, offset lithography relies on a delicate dance between ink and water, orchestrated by the principles of oil and water repulsion. The process begins with creating a printing plate containing the image to be reproduced. Traditionally, this plate is made of aluminum, with the image areas treated to attract oil-based inks and repel water, while the non-image areas do the opposite.
Once the plate is prepared, it undergoes a series of steps that lead to the transfer of the image onto the final printing surface. The plate is first dampened with water, adhering to the non-image areas due to their hydrophilic nature. Then, ink is applied to the plate, adhering exclusively to the image areas. The inked image is then transferred from the plate onto a rubber blanket, further maintaining the oil-water separation.
Finally, the rubber blanket makes contact with the paper or other printing material, and the image is offset onto the final surface. This indirect method of printing is what distinguishes offset lithography from direct printing methods, and it is this nuanced process that contributes to the method’s versatility and high-quality output.
Historical Significance of Offset Lithography
The roots of offset lithography can be traced back to the late 19th century, marked by the innovative contributions of individuals like Alois Senefelder, who is credited with the invention of lithography. Lithography, in its original form, involved drawing on a smooth stone surface with a greasy substance. It would then be chemically treated to allow for ink adhesion and repulsion, creating a print.
The offset variation of lithography evolved as a solution to the challenges of direct lithographic printing. By introducing the intermediary step of offsetting the image onto a rubber blanket before transferring it to the final surface, offset lithography addressed issues related to wear and tear on the printing plate and allowed for the efficient printing of large quantities.
The advent of offset lithography revolutionized the world of printing, further improving the mass production of newspapers, books, and various printed materials. Its efficiency, speed, and ability to reproduce intricate details contributed significantly to the growth of the printing industry in the 20th century and beyond.
Mechanics of Offset Lithography
Understanding the mechanics of offset lithography unveils its adaptability to diverse printing needs. Unlike other printing methods like large format printing or digital printing, offset lithography accommodates a wide range of printing surfaces beyond paper, including cardboard, metal, and plastic. This versatility makes it an ideal choice for producing a myriad of printed materials, from packaging to promotional materials and beyond.
The separation of the ink and water phases during the printing process results in sharp and clear images with vibrant colours. The offset method also allows for the printing of fine details, making it suitable for reproducing intricate artwork, photographs, and text with remarkable precision.
Additionally, offset lithography supports large-scale production runs, making it cost-effective for high-volume printing. The plates used in the process are durable and can withstand numerous impressions, contributing to the method’s efficiency and economic viability.
Enduring Relevance in the Digital Age
While the digital revolution has brought about significant changes in the printing industry, offset lithography maintains its relevance for specific applications. One of its key strengths lies in the production of high-quality, full-colour prints at a lower cost per unit for large quantities. This makes offset lithography particularly advantageous for tasks such as magazine, newspaper and book printing, where large volumes are often required.
Moreover, offset printing excels in colour consistency and accuracy, crucial factors for brand materials, packaging, and promotional items. The method allows for precise colour matching, ensuring the printed materials align with a brand’s established colour palette.
In an environmentally conscious era, the eco-friendly aspects of offset lithography add to its appeal. The use of oil-based inks and the longevity of printing plates contribute to a sustainable and efficient printing process, aligning with the growing demand for environmentally friendly practices.
While other printing types offer advantages in terms of short-run printing, customization, and quick turnaround times, offset lithography continues to carve its niche in the printing landscape, offering a balance between quality, cost-effectiveness, and environmental considerations.
The enduring legacy of offset lithography is apparent. From its humble beginnings in the 19th century to its continued relevance in the digital age, this printing method has proven itself as a reliable workhorse for mass production with uncompromised quality. Its adaptability, efficiency, and ability to produce vibrant, detailed prints on various surfaces make it a cornerstone of the printing industry. Offset lithography stands as a testament to the harmonious interplay of art, chemistry, and technology, maintaining its place as an integral part of the diverse and ever-evolving world of printing.
Consider consulting our industry experts at PRINTFINISH, attending trade shows, or reaching out to suppliers like Printers Parts and Equipment to gain insights and make informed decisions. Investing in high-quality, reliable printing equipment ensures that you can meet customer demands, maintain consistent print quality, and ultimately establish a solid reputation in the printing industry.